7 strategies for your profitable fleet
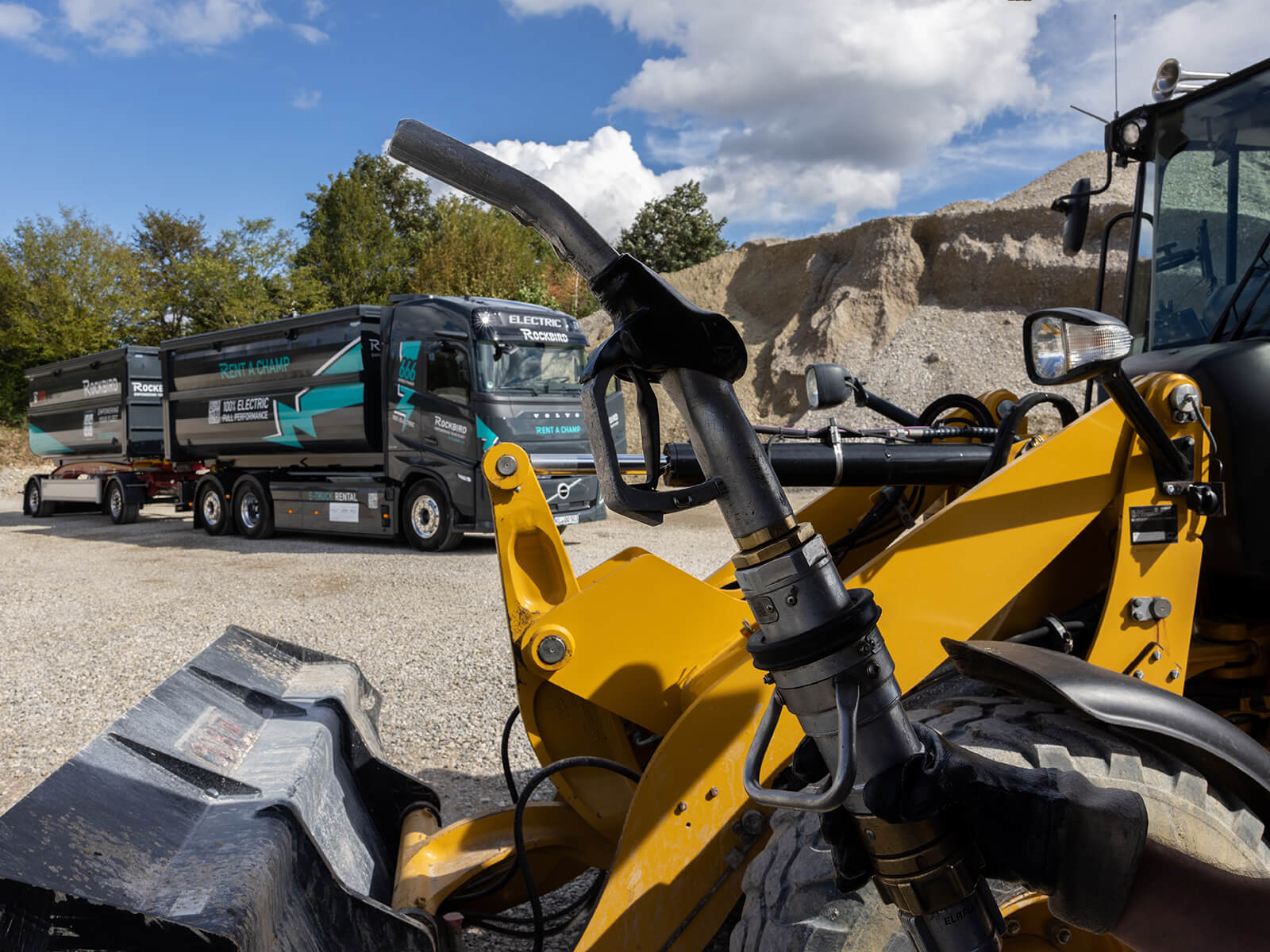
Goodbye cost explosion: Our top seven tips for more efficiency and sustainability in recycling & disposal.
Everything is becoming more expensive – not only consumers are noticing this in the supermarket or when it comes to heating bills, but also companies in particular. Rising energy costs, coupled with higher expenditure on materials and personnel and at the same time less well-filled order books, make doing business in times of crisis a real challenge. Saving costs is therefore the order of the day. But how can this best be implemented internally without compromising quality, profitability and employees? The good news is that in the recycling and waste management industry in particular, there are a number of things you can do to cut costs – sustainably and efficiently. We present seven strategies that will help you optimize your fleet and steer your company safely through uncertain times. Let’s go!
1. Into the future electrically
When it comes to electrically powered commercial vehicles, some prejudices persist: too unreliable, too complex, too expensive. However, manufacturers have made significant improvements in the development of their vehicles in recent years: They are now generally no more expensive than diesel-powered trucks and construction machinery, as their use is politically encouraged thanks to their zero emissions. In concrete terms, this means that subsidies are available and you save on fuel, road tax and tolls. Maintenance costs are also generally lower. The trend is clearly moving towards more electromobility, including in the transportation, recycling and construction sectors. So those who familiarize themselves with the new technology early on will have an easier time later on. With our rental options, you can add the new e-machines to your fleet – see the next point.
2. Rent instead of buying
Keyword e-fleet: The purchase of an e-truck or an electrically powered machine initially tears a big hole in the budget – money that many companies understandably do not want to invest at the moment. With our flexible rental models, you can expand your fleet in a targeted manner and save costs, as you only pay for what you use in the end – without risk or long-term liabilities. This means you can absorb order peaks and at the same time have no costs when the machines are not needed. At the same time, there is always a purchase option in case you want to invest in a new vehicle. The same naturally applies to our classic combustion engine machines: Choose your suitable commercial vehicle or construction machine from our large rental fleet – from tippers, tractor units and trailers to wheel loaders and material handlers.
3. Optimally configure vehicles and machines
Whether for transportation, handling or construction sites: every job is special and requires the right equipment. Our construction machinery and commercial vehicles are specially configured and optimized for use in recycling and waste disposal. This means you are optimally equipped for every challenge. Thanks to our many years of experience, we know the requirements of the industry and help you to increase performance and productivity while saving resources and costs.
4. Well-trained staff is half the battle
Whether classic diesel or electric, operating vehicles and construction machinery is not a matter of course and requires a high degree of technical understanding. Operating conditions are constantly changing in parallel with technical progress. Driver training is therefore an investment that is well spent in the long term: a driver who knows and understands his machine knows how to operate it with low wear and tear and in a resource-saving manner, and may also be able to carry out maintenance work independently. This increases the service life and therefore the productivity of your fleet.
5. Increase service life through regular maintenance
Speaking of maintenance: only a functioning fleet is efficient, because anything that stands idle unnecessarily causes costs in the long term. Therefore, make sure that machines do not break down in the first place by subjecting your fleet to regular inspections. This increases the service life and saves the purchase of expensive new machines. In addition to the prescribed maintenance in the workshop, you can help to ensure that your fleet is always up to date by carrying out regular inspections yourself. Having your own fleet officer (keyword “well-trained personnel”) can help you keep track of everything. Or take advantage of our external fleet management service: we can help you avoid downtime and unnecessary costs.
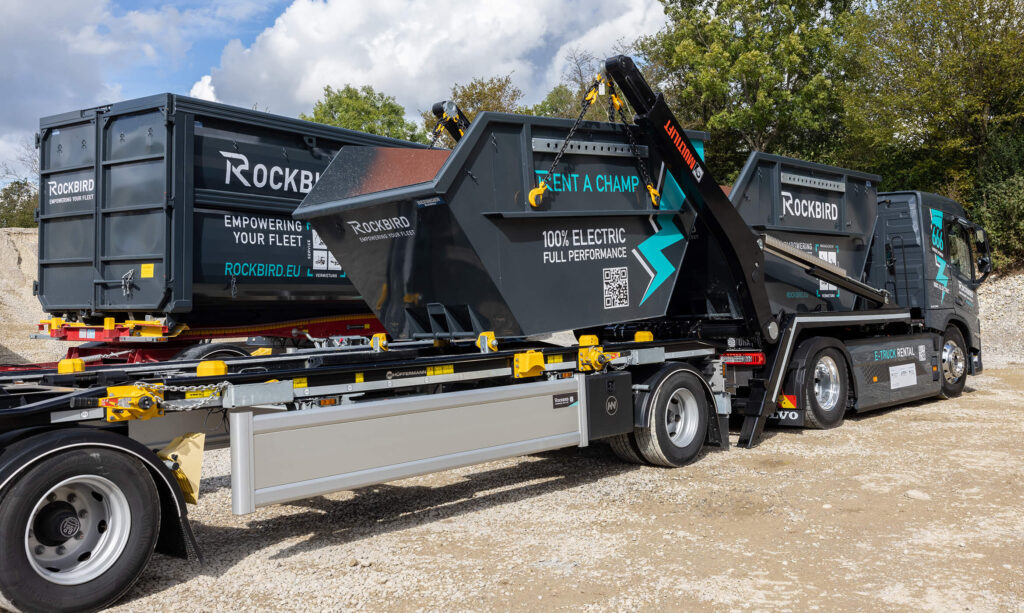
6. Make the most of the power of physics
What has long been common practice in the aviation industry also works in logistics, recycling and construction: Less resistance equals less effort equals lower energy consumption. In aircraft construction, aerodynamics uses the specially shaped profile of the wings so that the air flowing past them provides lift with increasing speed. In the same way, the power of physics can be used to minimize energy consumption elsewhere by aligning the front of the vehicle aerodynamically. Some manufacturers, such as Volvo and Mercedes, have already fitted aerodynamic front ends to some of their new trucks and have found that this can save a lot of fuel. This pays off particularly on longer distances that are covered at a constant speed. Conclusion: Progress sometimes starts with design.
7. Smart fleet management pays off
Whether it’s maintenance, route planning or administration, you can’t go wrong with digital fleet management. How long has my machine been parked, when and how exactly is it being used and how long does it run during its respective assignments? When is the next inspection due? If you keep a digital record of this, you can recognize patterns in use, downtime and maintenance intervals at a glance and can therefore optimally coordinate operations or prevent damage before it occurs. What may seem time-consuming at first glance becomes a routine over time, helping you to operate more cost-effectively. With our 360-degree advice, our experts will be happy to help you set up the appropriate tools in your company – independently of the manufacturer and in a neutral manner.
Conclusion: step by step to cost optimization
Our overview shows that many small steps add up to make a big difference. You don’t necessarily have to cut costs – it’s enough to pull a small lever here and there to make a big difference. It’s worth trying it out!
Are you ready
for the future?
Do you want to make your company fit for the future and find out more about the changes that make sense?
Contact us – our experts will be happy to advise you.